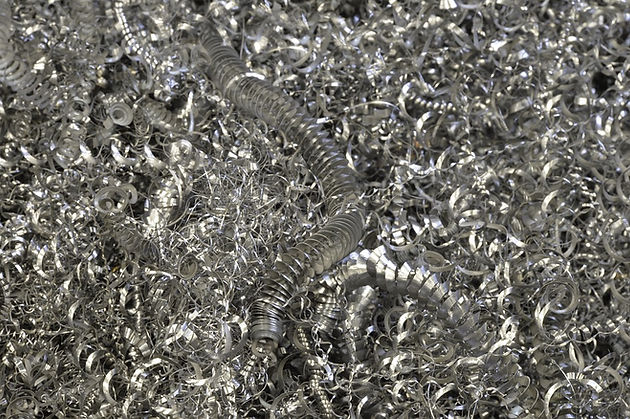
We convert chip wastes
into a high value commodity
Contract Mechanical Milling & Powderization
Ask how we can convert your segregated chips & turnings into 3D printing powder
that you can use at your facility.
​
Commercial & Academic R&D Production
For validation ahead of full scale manufacturing.
​
System Design & Integration
Turnkey design, installation & integration, allowing manufacturers to increase
the value of their operations by converting valuable wastes into powders.
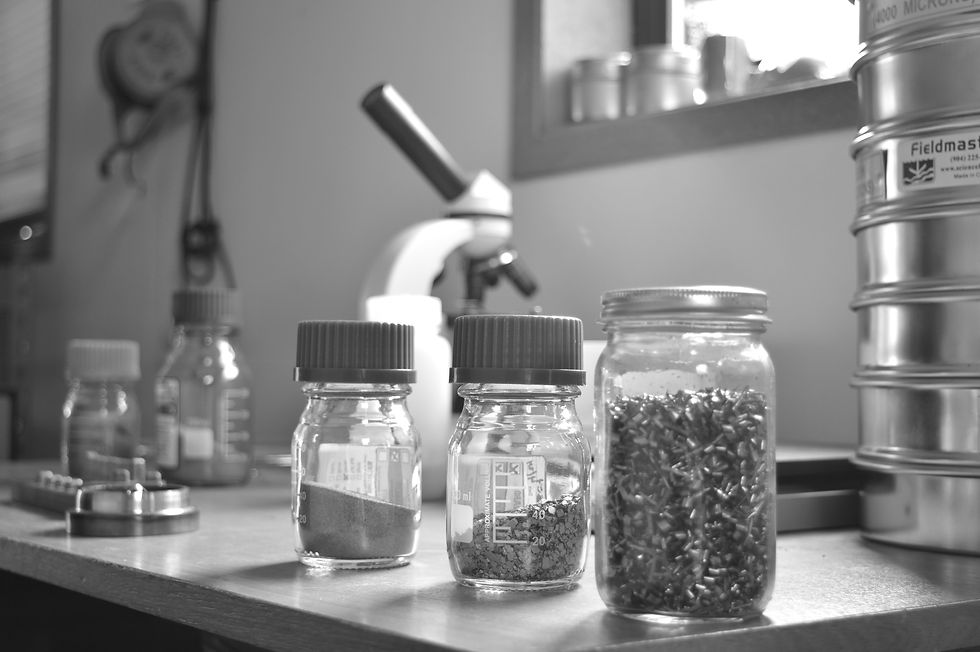
Industrial Scale Chip Waste Conversion
Today's additive manufacturing industry often depends on expensive, specialized materials to meet the demands of cutting edge aerospace and medical applications.
State of the art gas and water atomization facilities consume enormous amounts of energy, inert gas, and purified water to produce the uniform metal powders that fuel growth in the industry.
But what if there was a different way to produce these expensive, specialized materials?
One that could meet the emerging demands in automotive, industrial, oil & gas, solar and consumer product manufacturers?
A simple process built upon well understood, low cost mechanical tech, already on the shop floor.
​
Easily integrated with existing operations, minus the enormous capital equipment costs and specially trained personnel.
We've developed the process, and you don't need to be a rocket scientist to make it work for you.

Reference nozzle printed with recycled REAlloy 304L powder on
a DMG Mori Lasertec 65 Hybrid
Advantages of Mechanical Milling

Significantly lower capital investment than
gas & water atomization facilities. Large ROI (4.72)
​
No special permits required. Swarf pre-processing and mechanical milling technologies are similar to what's on your shop floor.
Easy integration.
Powders are immediately usable for tooling, molding and other
low-end applications.
​
Equipment can be remotely monitored for 24-7, lights out operation.
Fewer hazards. Low or no inert gases required. Low water use.
Low electricity use. No hazardous chemicals or solvents.
Modular. Increase output by adding more production cells.
​
Can produce a wide range of industrial alloy powders.
​
Easy to maintain. Parts are widely available.
.jpg)